- Visibility 254 Views
- Downloads 35 Downloads
- DOI 10.18231/j.ijodr.2024.029
-
CrossMark
- Citation
3D printing: Changing the landscape of orthodontics
Introduction
Over the past few years, the utilization of three-dimensional (3D) printing technology in medical and dental fields has witnessed a significant surge. This burgeoning interest stems from the potential it holds for personalized medical and dental solutions, cost savings in small-scale production, streamlined storage, sharing, and processing of patient image data, as well as its educational enhancements.[1]
Three-dimensional printing, stands at the forefront of contemporary digital dentistry. Charles Hull marked a significant milestone in 1983 by producing the first-ever 3D object through printing, thus setting the stage for a transformative journey in manufacturing technology.[2] Essentially, 3D printing involves the creation of three-dimensional solid objects from digital files. The process, also referred to as additive manufacturing or desktop fabrication, revolves around the conversion of digital 3D models, typically saved in Surface Tessellation Language (STL) format, into tangible objects through layer-by-layer deposition.[3]
The applications of 3D printing span across various medical and dental domains, including medical modeling, surgical guide fabrication, prosthodontics, restorative dentistry, orthodontics, implantology, and instrument manufacturing.[4]
The advent of digital solutions has ushered in a paradigm shift in diagnosis and treatment planning, transitioning from traditional two-dimensional approaches to advanced three-dimensional techniques. The incorporation of digital technology caters to the evolving needs of multi-doctor practices, diverse practice locations, and burgeoning patient volumes, facilitating efficient storage, retrieval, and sharing of information.[5]
Recent advancements in digital technology, including digital cephalometric X-rays, digital photography, digital impressions, intraoral and facial scanners, cone-beam computed tomography (CBCT), and 3D printing, have significantly enhanced the efficiency, accuracy, consistency, and predictability of treatment outcomes. The introduction of computer-aided design and computer-aided manufacturing (CAD/CAM) systems in the dental field further underscores the transformative potential of digital technologies. In particular, the advent of digital intraoral impression devices has enabled the capture of high- resolution 3D virtual models, eliminating the drawbacks associated with conventional dental impressions. These digital models offer versatile options for designing and manufacturing various dental restorations, implants, study models, and orthodontic appliances, ranging from customized brackets to aligners and retainers.
Integration with cloud-based technology further amplifies the capabilities of digital intraoral scanners, facilitating secure transmission and storage of scanned images for diagnostic purposes.[6]
In essence, the amalgamation of 3D printing technology with digital advancements and cloud computing heralds a new era in medical and dental practice, characterized by enhanced precision, efficiency, and accessibility across diagnostic, treatment planning, and manufacturing processes ([Figure 1]).
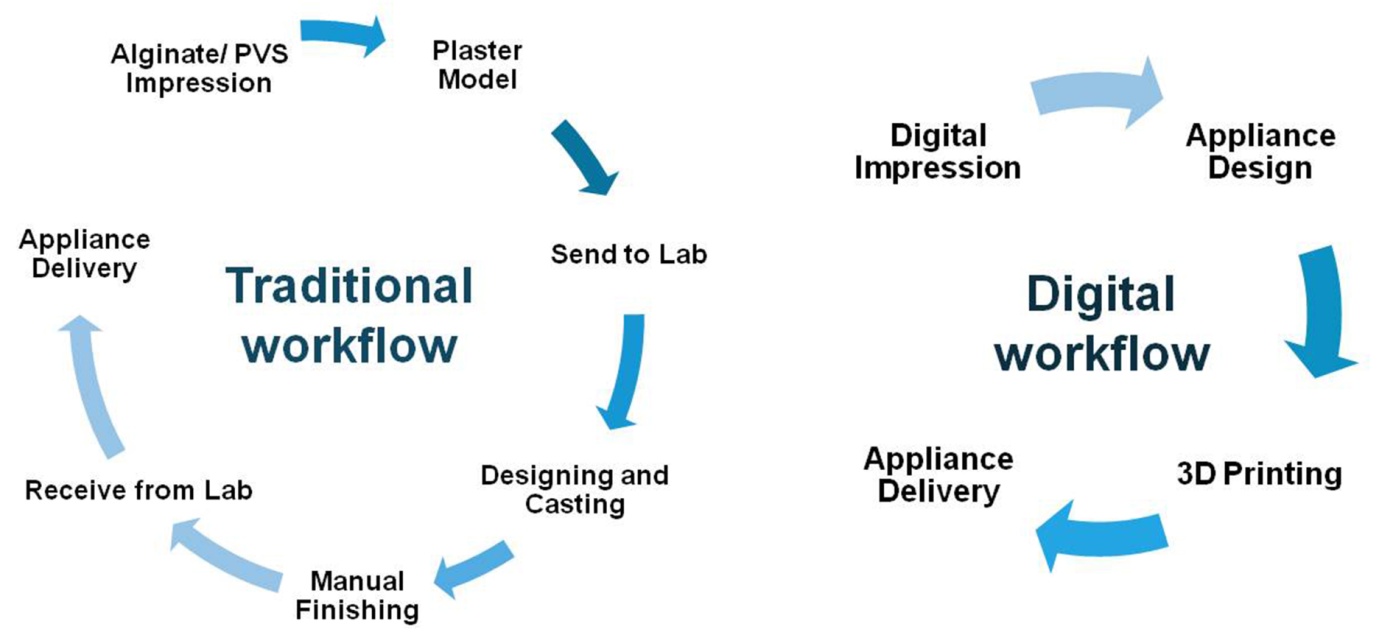
Discussion
History of 3d printing
1940s-70s: The idea
In 1945, Murray Leinster's, in his short story "Things Pass By," remarkably foreshadowed the essence of 3D printing technology by envisaging a machine capable of translating drawings into tangible 3D objects through the use of melted plastic and a moving arm mechanism. In 1974, an article by David Jones provided a prescient description of the stereolithography process, fueling the discourse and laying the conceptual groundwork for subsequent developments in the field. [7], [8]
1984-1988: The invention of stereolithography
In 1983 with the pioneering work of Charles Hull, often hailed as the father of modern 3D printing was successful in printing a three-dimensional object for the first time and introduced the world to the revolutionary concept of stereolithography. In 1984, Hull filed a patent for a stereolithography system, which was granted approval in 1986, leading to the establishment of 3D Systems, a company dedicated to advancing the frontiers of 3D printing technology. [7], [9]
The year 1988 witnessed further milestones in the evolution of 3D printing, with the introduction of selective laser sintering (SLS) and fused deposition modeling (FDM) technologies.
In 1993, MIT professor Emanuel Sachs coined the term "3D Printing," formally known as additive manufacturing. In 1995, Zcorp obtained an agreement with MIT to create starch and plaster models, further propelling 3D printing into the commercial domain. [7], [10]
2000s: The market comes to the masses
The dawn of the 21st century witnessed a democratization of 3D printing technology, with significant strides made towards accessibility and affordability. The introduction of the first commercially available desktop 3D printer by Objet in 2006 marked a pivotal moment, enabling at-home hobbyists to explore the possibilities of 3D printing with unprecedented ease. [7]
Patents end and consumer accessibility
The expiration of key patents in 2009, including those for SLA and FDM technologies, opened the floodgates for innovation and competition within the 3D printing market. Formlabs made a significant breakthrough in 2012 with the launch of the Form 1, the first realistically affordable SLA printer for consumers, catalyzing further advancements and widespread adoption of 3D printing technology. [7] The evolution of 3D printing is depicted in ([Figure 2]).
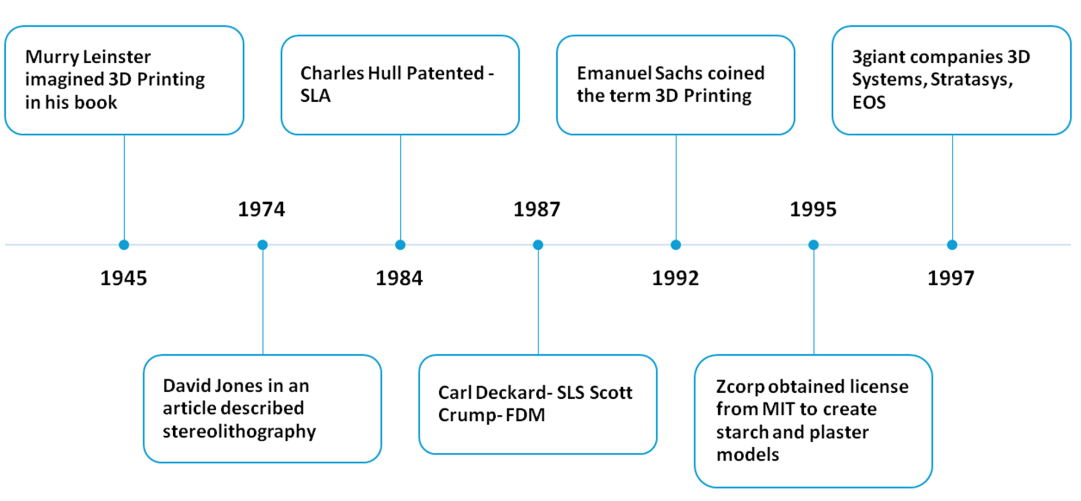
Key additive technologies
The realm of manufacturing has witnessed a transformative evolution with the advent of 3D printing, also known as additive manufacturing. Unlike traditional subtractive methods, which involve carving out a desired shape from a larger block of material, additive manufacturing entails the layer-by-layer deposition of material to construct a three-dimensional object ([Figure 3]). Both approaches offer distinct advantages and find applications tailored to specific user requirements. [7], [10], [11], [12]
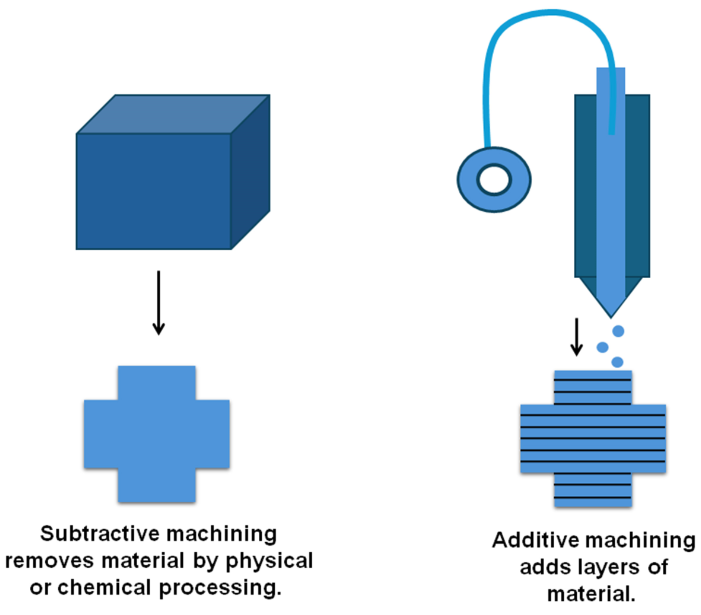
Several additive technologies have emerged as cornerstones of 3D printing, each offering unique capabilities and applications ([Figure 4]):
Fused deposition modelling (FDM)
This technique, pioneered by S. Scott Crump in the late 1980s, involves the extrusion of thermoplastic materials to create intricate structures. FDM finds applications in prototyping and scaffold manufacturing for tissue engineering. [8], [11], [13], [14]
Selective laser melting (SLM) and Selective laser sintering (SLS)
Laser-based additive manufacturing methods utilize high-energy laser beams to fuse metallic or polymeric powders, enabling the fabrication of complex geometries and functional components. [8], [11], [15], [16]
Electron beam melting (EBM)
EBM technology harnesses electron beams to create fully dense metal parts with exceptional strength and porosity, making it ideal for orthopaedic and surgical implant manufacturing. [8], [11]
Stereolithography (SLA)
SLA, pioneered by Charles W. Hull in 1986, employs ultraviolet laser light to solidify resin layers, producing high-resolution prototypes and medical models with exceptional accuracy. [8], [11]
Poly jet printing (PPP) and binder jetting
Both use same type of printhead technology but while Poly jet uses a liquid resin which is deposited out of hundreds of nozzles and immediately cured with ultraviolet light, binder jetting uses a liquid binding agent selectively deposited to powder particles in a bed. [8], [11]
Digital light processing (DLP)
DLP technology utilizes digital micro-mirror devices to project UV light onto liquid resin, enabling rapid and precise object fabrication with superior resolution and surface finish. [1], [8]
Laminated object manufacturing (LOM)
Laminated Object Manufacturing (LOM) combines additive and subtractive techniques to produce large, dimensionally accurate parts from materials such as plastics, paper, and ceramics. [8], [12]
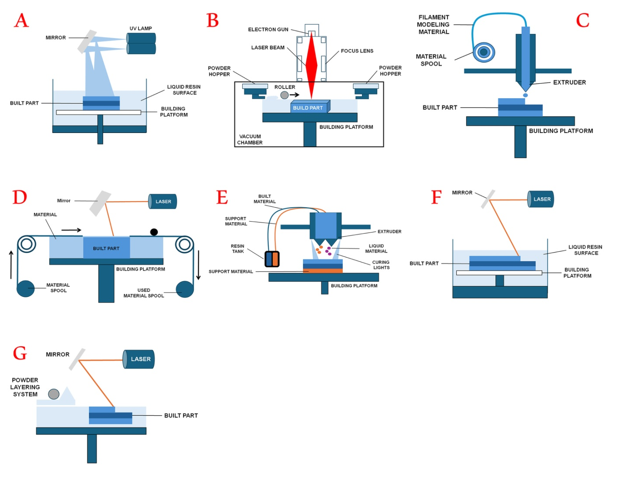
Workflow
The seamless creation of patient-specific 3D models involves a structured workflow comprising multiple steps, each crucial for ensuring precision and efficacy ([Figure 5]).
Service request/Order process
The process initiates with physicians identifying the need for a patient-specific model and submitting a request for the service. This process involves gathering essential information such as patient identity, clinical diagnosis, imaging details, and the intended use of the model. Requests can be received through various channels, including hospital systems, email, or physical forms.
Image data acquisition
Volumetric image data acquired through diagnostic imaging modalities such as CT, MRI, or echocardiography serves as the foundation for 3D reconstruction. Recent advancements include the use of 3D scanning to collect surface contour data, particularly in dental and maxillofacial applications. [8]
3D Biomodelling
The virtual model derived from image reconstruction undergoes optimization for 3D printing. This phase involves refining the model, eliminating non- printable parts, smoothing surfaces, and enhancing structural integrity. [17]
Physician approval process
Final images of the preprint model are reviewed by the referring physician to ensure alignment with patient requirements. Approval methods include presentation formats, 3D PDFs, or specialized software like MIMICS viewer, facilitating comprehensive evaluation and feedback exchange. [8], [17]
3D Printing and post processing
The approved virtual model undergoes layer-by-layer printing to produce a tangible physical replica of the anatomy. Post- printing, support materials are removed to reveal the clean final model ready for use.
Labeling, packaging, and delivery
Each 3D printed part is labeled with patient and physician identities, manufacturing date, and material details for easy identification.
Post-delivery surveillance
Feedback collection from end-users facilitates continuous improvement of services and processes.[8]
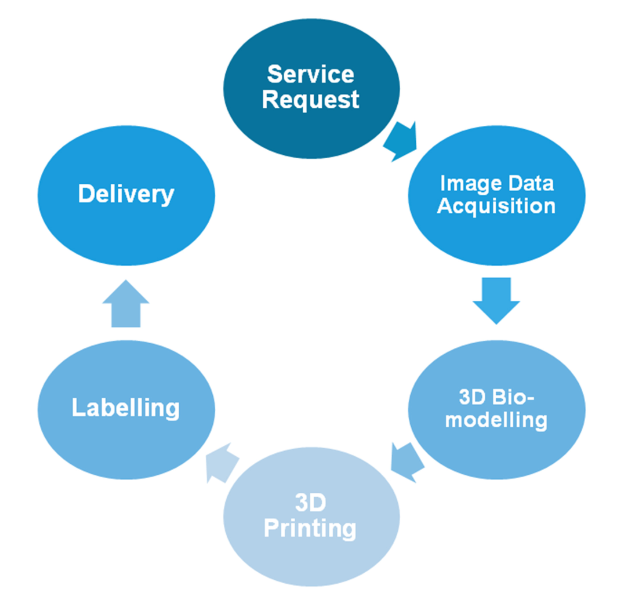
Data Acquisition
Intraoral scanners
Intraoral scanners stand at the forefront of dental technology, representing a significant departure from traditional impression techniques. These cutting-edge devices employ advanced optical scanning methods to capture detailed three-dimensional images of the oral cavity, revolutionizing the way dental professionals gather crucial diagnostic data and plan patient treatments. The journey of intraoral scanners began in 1987 with the introduction of three-dimensional digital impressions by CEREC 1, utilizing infrared cameras and optical powder on the teeth. [18] By utilizing optical components such as confocal laser scanning microscopy (CLSM), optical triangulation, and optical coherence tomography (OCT), these scanners capture detailed images of the dentition with exceptional clarity and precision.
Examples include the iTero® scanner, which utilizes confocal laser scanner microscopy, and the 3Shape TRIOS®, which also operates on the principle of confocal microscopy but with a fast-scan rate. Additionally, scanners such as the Lythos™ Digital Impression System and the CS 3500 by Carestream Dental employ fringe interferometry and confocal laser scanner microscopy, respectively, to capture detailed 3D data of the dentition.[19], [20]
Superiority of digital impressions over traditional impressions- Conventional impression materials are fraught with limitations, including complex workflows, poor dimensional stability, and patient discomfort. In contrast, intraoral scanners offer a non-contact optical solution that eliminates these drawbacks, providing clinicians with highly accurate digital impressions in a fraction of the time. [19], [20]
Orthodontic applications and advantages of intraoral scanners- In orthodontics, intraoral scanners offer a wide array of applications, ranging from digital storage of study models to advanced software for cast analysis and treatment planning. Clinicians can leverage these scanners to perform tasks such as landmark identification, arch width and length measurements, and evaluation of occlusion with unparalleled precision. Moreover, intraoral scanners facilitate seamless integration with various digital workflows, enabling clinicians to collaborate with third-party providers and incorporate cone-beam computed tomography (CBCT) data for advanced treatment modalities. [19]
Validation and clinical impact of intraoral scanners- Extensive research has validated the accuracy and reliability of intraoral scanners, with many studies demonstrating comparable or superior performance compared to conventional impressions. Clinicians have reported significant improvements in efficiency and workflow with intraoral scanners, with digital impressions often outperforming traditional methods in terms of procedural duration and patient satisfaction. [21]
Desktop 3D scanners
Desktop 3D scanners employ non-destructive laser beams and digital cameras to capture high- resolution images of dental impressions and physical casts. These scanners are equipped with automated platforms that rotate and incline the target objects during scanning, ensuring comprehensive coverage of the model's geometry from multiple angles.
Some of the key desktop scanner systems are listed below.
Ortho Insight 3D™ (Motion View Software, LLC): Introduced in 2012, Ortho Insight 3D™ offers a robotic scan with exceptional accuracy (40-200 microns). Ortho Insight 3D™ software provides features such as digital storage of patient records, cast analysis, treatment planning, and optional modules for indirect bonding and cephalometrics.
3 Shape Desktop Scanners (Copenhagen, Denmark): The R500 and R700 series utilize red light laser technology with high accuracy (20 microns), while the R900 series employs blue LED laser technology for even greater precision (15microns). These scanners are suitable for orthodontic offices and labs of different sizes, with scanning times ranging from 1 to 7 minutes depending on the model.
Maestro 3D (AGE Solutions, Piza, Italy): It has LED projector and digital cameras, offering high-resolution scans with 10 microns accuracy. The system includes software modules for inspection, editing, tooth measurements, arch analysis, virtual setup, and export for 3D printing.[6]
Validation and clinical impact of digital scanners- Studies have validated the precision and reliability of desktop 3D scanners for dental applications, with comparisons to traditional plaster models yielding small mean differences (< 0.20 mm). While certain desktop scanners exhibit higher precision in areas with complex curvature, they may demonstrate lower accuracy in reproducing interdental spaces, highlighting the importance of careful evaluation and calibration. [22]
Software’s for 3d modeling application
The realm of 3D printing is accompanied by a diverse array of software tools, each playing a crucial role in the journey from a digital model to a tangible printed object. Let's explore the different classes of 3D printing software and their functionalities ([Figure 6]).
3D design software
CAD software, such as Fusion 360 and FreeCAD, is tailored for precise hard body modeling, ideal for engineering applications where dimensional accuracy is paramount. On the other hand, 3D modeling software like ZBrush and Blender specializes in soft body modeling, enabling the creation of organic shapes and characters through sculpting techniques.
Editing and repairing 3D printing software
Often, 3D models are obtained in STL format, which may contain defects affecting print quality. STL file editing and repair tools allow users to visualize, modify, and rectify these issues, ensuring that the models are optimized for successful 3D printing.
Printable file analysis
Printable file analysis tools facilitate quick and comprehensive examination of sliced files, providing valuable insights without the need for extensive slicing software.
Slicing software
Slicing software plays a pivotal role in the converting 3D model files into machine-readable G-code. Slicers generate G-code instructions that guide the printer in constructing each layer, ultimately realizing the digital model in physical form.
3D printer host
Acting as the bridge between your computer and the 3D printer. It transmits G-code instructions to the printer, monitors the printing process, and allows real-time adjustments to settings. Often, the functionalities of a slicer and a printer host are integrated into unified 3D printing software solutions. [23]
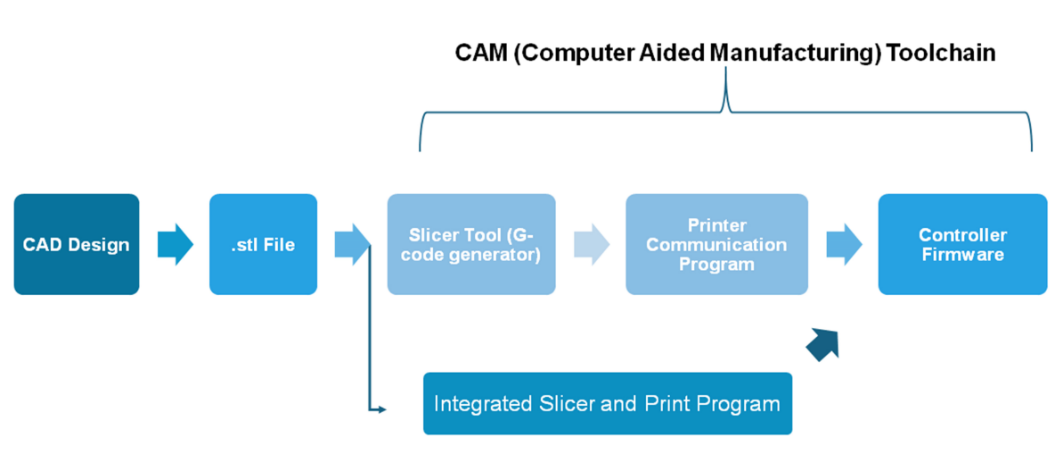
3D Printers
Stratasys, ltd
In orthodontics, Stratasys printers like the Objet30 OrthoDesk have gained prominence for their ability to produce high-quality orthodontic models with exceptional surface finish. These printers utilize PolyJet technology and offer materials such as VeroDentPlus, MED610, and VeroGlaze, each suitable for specific orthodontic applications.
3D systems
The ProJet® 3510 MP series by 3D Systems is renowned for its capability to deliver uniformly accurate thin wax-ups for crowns, bridges, and partial dentures. These professional printers support the VisiJet® line of materials, including Dentcast, PearlStone, Stoneplast, and VisiJet® S300, designed to meet a wide range of dental applications with precision and reliability.
Envision TEC
EnvisionTEC's Ultra 3SP Ortho printer is engineered specifically for dental use, employing proprietary 3SP (Scan, Spin, Selectively Photocure) technology to achieve superior print speeds and surface finish. The Ultra 3SP Ortho printer support materials such as E-Denstone, ABS 3SP White, ABS-like plastic, and E-Glass, catering to diverse clinical needs with enhanced efficiency and accuracy.
MakerBot and FDM printers
Fused Deposition Modeling (FDM) printers, including the MakerBot Replicator 2, have emerged as cost-effective solutions for orthodontic practices seeking affordable 3D printers. While FDM printers offer a smaller initial investment and lower material costs, they may exhibit limitations in surface finish due to larger layer sizes. [6], [11]
Printing materials
The selection of printing materials plays a pivotal role in determining the performance and suitability of 3D printed orthodontic appliances. Materials such as VeroDentPlus, Dentcast, and E-Denstone offer varying properties tailored to specific clinical requirements, including biocompatibility, durability, and esthetics ([Figure 7]). [8], [11]
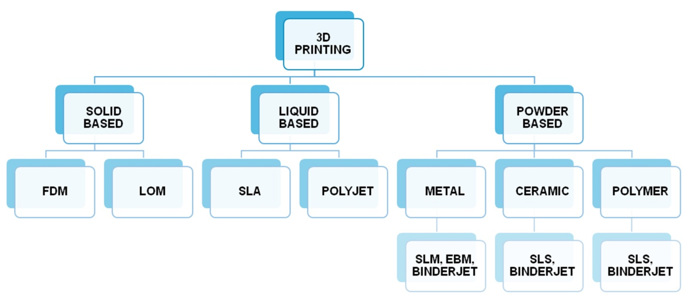
Applications of 3D Printing
3D printing, has witnessed widespread adoption across diverse industries, revolutionizing traditional manufacturing processes and unlocking new possibilities for innovation and customization. From aerospace to healthcare, this technology has found applications that range from prototyping to mass customization, offering benefits such as reduced lead times, cost savings, and enhanced product performance. Applications of 3D printing across different industries are listed below.
Aerospace
The aerospace industry has embraced 3D printing for manufacturing various components of aircraft and spacecraft. Companies like Boeing and NASA have utilized this technology to produce interior parts, rocket engines, and components for satellites.[24], [25]
Automotive industry
The automotive sector has reaped significant benefits from additive manufacturing, leveraging it to create lighter parts with complex geometries. Automotive companies have embraced design customization and innovation, enhancing their product offerings and staying competitive in the market.[8], [11]
Architecture
In the field of architecture, 3D printing holds the potential to revolutionize construction processes by enabling the creation of houses using robotics with minimal human intervention. This technology is instrumental in both construction and design phases, promising affordable housing solutions in shorter timeframes.[8], [24]
Shoe industry
3D printing has disrupted the traditional methods of shoe manufacturing by enabling mass customization for ergonomics and exclusivity. The collaboration between Adidas and Carbon resulted in the launch of Futurecraft 4D, showcasing the potential of additive manufacturing in the shoe industry.[8]
Food industry
The food industry has also embraced 3D printing for its ability to customize food designs, offer personalized nutrition, simplify supply chains, and enhance food product availability. The technology holds promise for revolutionizing food production and catering to individual dietary needs.[8], [26]
Jewellery industry
3D printing has empowered the jewellery industry to create intricate designs and offer unique, customizable options to consumers. By leveraging 3D technology, jewellery makers can produce items on demand, reducing inventory costs while catering to consumer preferences for personalized jewellery pieces.[8], [27]
Healthcare
In healthcare, 3D printing has emerged as a transformative tool for producing medical devices, prosthetics, and anatomical models with unparalleled precision. From hearing aids to orthopaedic implants, the technology enables the customization of medical solutions to fit individual patient needs. Ongoing research explores bio printing applications for tissue engineering and surgical planning, promising breakthroughs in patient care and treatment outcomes.[3], [8], [28]
Consumer market
While the consumer market for 3D printing is still evolving, enthusiasts and hobbyists are driving innovation through thousands of projects and experiments. While challenges remain in competing with mass production economies, the consumer sector holds promise for widespread adoption of 3D printing technology.[29]
In the realm of dental and orthodontic care, 3D printing has ushered in a new era of precision, efficiency, and customization, revolutionizing traditional treatment processes and enabling clinicians to deliver enhanced patient outcomes.
Let’s look into dental and orthodontic applications of 3D printing.
Clear aligner manufacturing
Clear aligner therapy relies heavily on 3D technologies such as cone-beam computed tomography (CBCT) and intraoral scanners. Orthodontists use intraoral scanners to create 3D models of patients' mouths, enabling them to digitally plan orthodontic movements and simulate treatment outcomes. Subsequently, these digital models are converted into STL files and 3D printed to produce a series of aligner trays tailored to each patient's treatment plan. By leveraging 3D printing, orthodontists can achieve gradual orthodontic movement, resulting in the desired alignment of teeth over time.[28]
Surgical guide technique for miniscrew placemen
3D printing enables the creation of surgical guides based on CBCT scans and digital models, allowing orthodontists to pinpoint the optimal placement sites for miniscrews with unparalleled accuracy. These guides facilitate controlled placement, minimize risks, and streamline the miniscrew insertion process, enhancing treatment outcomes and patient comfort.
Corticotomy technique using 3D Printed surgical guides
With 3D printing, orthodontists can create surgical guides with precise micro-incision lines, allowing for controlled and minimally invasive corticotomy procedures. These custom surgical guides, fabricated based on digital impressions and CBCT data, ensure accurate osteotomy placement, optimize treatment outcomes, and enhance patient comfort during the recovery process.
Orthognathic surgery 3D planning
3D planning using CBCT and digital models enables orthodontists to simulate surgical movements in three dimensions, identify relevant anatomical structures, and plan surgical interventions with greater accuracy. Surgical 3D printed splints aid in guiding surgical cuts, placement of screws, and orthognathic realignment, ensuring precise execution of treatment plans and improved patient outcomes.
Retention and outcome assessment
3D technology facilitates the design and fabrication of various orthodontic retainers, including fixed lingual retainers and removable appliances, with unparalleled precision. Additionally, 3D-printed models serve as valuable tools for outcome assessment, enabling clinicians to evaluate treatment efficacy and make informed decisions regarding further interventions.[30], [31]
Conclusion
In conclusion, the rapid advancement of three-dimensional technologies in orthodontics has revolutionized treatment workflows and patient care. These innovations enable orthodontists to optimize their time and knowledge, delivering superior treatment outcomes through digital design and 3D printing of orthodontic appliances. As these technologies continue to develop, orthodontists are poised to further enhance patient care and treatment outcomes. [3], [6]
Search Methodology
We conducted a thorough manual search of electronic databases like PubMed, Scopus, Science Direct, and Web of Science. Our review focuses on thirty-one articles, examining topics related to "Digital Orthodontic," "3D Printing," "Additive Manufacturing," "Intraoral Scanners," "Digital Impressions," "Desktop Scanners," "CAD-CAM," and "Orthodontic."
Statement of Informed Consent and Ethical Approval
Informed consent and Ethical clearance are not applicable as it does not include any animal or human research.
Data Availability Statement
The study did not report any data.
Author Contributions
Prasad Konda - Conceptualization, Writing- Review & Editing
Afaf M Rafiq - Data Acquisition, Writing- Original Draft Preparation.
Conflict of Interest
The authors declare no conflicts of interest.
Source of Funding
None.
References
- G Oberoi, S Nitsch, M Edelmayer, K Janjić, A S Müller, H Agis. 3D Printing-Encompassing the Facets of Dentistry. Front Bioeng Biotechnol 2018. [Google Scholar] [Crossref]
- C Zaharia, A Gabor, A Gavrilovici, A Stan, L Idorasi, C Sinescu. Digital Dentistry - 3D Printing Applications. J Interdiscip Med 2017. [Google Scholar]
- S Mahamood, MA Khader, H Ali. Applications of 3-D printing in orthodontics: A Review. Int J Sci Stud 2016. [Google Scholar]
- S Prasad, NA Kader, G Sujatha, T Raj, S Patil. 3D printing in dentistry. J 3D Print Med 2018. [Google Scholar]
- CS Favero, JD English, BE Cozad, JO Wirthlin, MM Short, FK Kasper. Effect of print layer height and printer type on the accuracy of 3- dimensional printed orthodontic models. Am J Orthod Dentofacial Orthop 2017. [Google Scholar]
- E Taneva, B Kusnoto, CA Evans, F Bourzgui. 3D Scanning, Imaging, and Printing in Orthodontics. Issues in Contemporary Orthodontics 2015. [Google Scholar]
- J Haines. History of 3D printing: When was 3D printing invented? [Internet]. All3DP. 2024. [Google Scholar]
- RP Kaul, J Parthasarthy. . Fundamentals of 3D Printing Technology for Medical & Dental Professionals [Internet]. Kindle eBooks 2021. [Google Scholar]
- D Sumasri, G Khanna, S Srimukhi. 3d Printing - A Boon to Dentistry. Sch J Dent Sci 2018. [Google Scholar]
- B Berman. 3-D printing: The new industrial revolution. Bus horiz 2012. [Google Scholar]
- C Groth, ND Kravitz, PE Jones, JW Graham, WR Redmond. Three-dimensional printing technology. J Clin Orthod 2014. [Google Scholar]
- A Aydin, F Kahraman, V Ivkovic, M Turhan. Can human beings produce everything? The limits of 3D printer. Research & Reviews in Engineering- Summer 2019 2021. [Google Scholar]
- J Winder, R Bibb. Medical rapid prototyping technologies: state of the art and current limitations for application in oral and maxillofacial surgery. J Oral Maxillofac Surg 2005. [Google Scholar]
- I Zein, DW Hutmacher, KC Tan, SH Teoh. Fused deposition modeling of novel scaffold architectures for tissue engineering applications. Biomaterials 2002. [Google Scholar]
- JT Rimell, PM Marquis. Selective laser sintering of ultra-high molecular weight polyethylene for clinical applications. J Biomed Mater Res 2000. [Google Scholar]
- GD Giacomo, J Silva, R Martines, S Ajzen. Computer-designed selective laser sintering surgical guide and immediate loading dental implants with definitive prosthesis in edentulous patient: A preliminary method. Eur J Dent 2014. [Google Scholar]
- ND Kravitz, C Groth, T Shannon. CAD/CAM software for three-dimensional printing. J Clin Orthod 2018. [Google Scholar]
- SB Patzelt, A Emmanouilidi, S Stampf, JR Strub, W Att. Accuracy of full-arch scans using intraoral scanners. Clin Oral Investig 2014. [Google Scholar]
- S Logozzo, EM Zanetti, G Franceschini, A Kilpelä, A Mäkynen. Recent advances in dental optics - Part I: 3D intraoral scanners for restorative dentistry. Opt Lasers Eng 2014. [Google Scholar] [Crossref]
- F Prati, E Regar, GS Mintz, E Arbustini, CD Mario, IK Jang. Expert review document on methodology, terminology, and clinical applications of optical coherence tomography: physical principles, methodology of image acquisition, and clinical application for assessment of coronary arteries and atherosclerosis. Eur Heart J 2010. [Google Scholar]
- D Naidu, TJ Freer. Validity, reliability, and reproducibility of the iOC intraoral scanner: a comparison of tooth widths and Bolton ratios. Am J Orthod Dentofacial Orthop 2013. [Google Scholar]
- S Akyalcin, DJ Dyer, JD English, C Sar. Comparison of 3-dimensional dental models from different sources: diagnostic accuracy and surface registration analysis. Am J Orthod Dentofacial Orthop 2013. [Google Scholar]
- . All3DP. The best free 3D printing software in 2024 [Internet]. All3DP. 2024. [Google Scholar]
- O Hooper. 3D Printing and Architecture [Internet]. Machine design. 2020. [Google Scholar]
- C Munoz, C Kim, L Armstrong. Layer-by-Layer: Opportunities in 3D printing technology trends, growth drivers and the emergence of innovative applications in 3D printing [Internet]. Toronto Metropolitian University: MaRS Market Insights. 2013. [Google Scholar]
- N Nachal, JA Moses, P Karthik, C Anandharamakrishnan. Applications of 3D Printing in Food Processing. Food Eng Rev 2019. [Google Scholar]
- . Guide to jewelry 3D Printing [Internet]. Industry insights: Formlabs. 2019. [Google Scholar]
- S Sharma, SA Goel. Three-Dimensional Printing and its Future in Medical World. J Med Res and Innov 2019. [Google Scholar]
- G Harmon. Three-Dimensional Printing and its Future in Medical World. 2020. [Google Scholar]
- I Francisco, MP Ribeiro, F Marques, R Travassos, C Nunes, F Pereira. Application of Three-Dimensional Digital Technology in Orthodontics: The State of the Art. Biomimetic 2022. [Google Scholar] [Crossref]
- ED Taneva, A Johnson, G Viana, CA Evans. 3D evaluation of palatal rugae for human identification using digital study models. J Forensic Dent Sci 2015. [Google Scholar]
- Introduction
- Discussion
- History of 3d printing
- 1940s-70s: The idea
- 1984-1988: The invention of stereolithography
- 2000s: The market comes to the masses
- Patents end and consumer accessibility
- Key additive technologies
- Fused deposition modelling (FDM)
- Selective laser melting (SLM) and Selective laser sintering (SLS)
- Electron beam melting (EBM)
- Stereolithography (SLA)
- Poly jet printing (PPP) and binder jetting
- Digital light processing (DLP)
- Laminated object manufacturing (LOM)
- Workflow
- Data Acquisition
- Intraoral scanners
- Desktop 3D scanners
- Software’s for 3d modeling application
- 3D design software
- Editing and repairing 3D printing software
- Printable file analysis
- Slicing software
- 3D printer host
- 3D Printers
- Printing materials
- Applications of 3D Printing
- Aerospace
- Automotive industry
- Architecture
- Shoe industry
- Food industry
- Jewellery industry
- Healthcare
- Consumer market
- Clear aligner manufacturing
- Surgical guide technique for miniscrew placemen
- Corticotomy technique using 3D Printed surgical guides
- Orthognathic surgery 3D planning
- Retention and outcome assessment
- Conclusion
- Search Methodology
- Statement of Informed Consent and Ethical Approval
- Data Availability Statement
- Author Contributions
- Conflict of Interest
- Source of Funding
How to Cite This Article
Vancouver
Konda P, Rafiq AM. 3D printing: Changing the landscape of orthodontics [Internet]. IP Indian J Orthod Dentofacial Res. 2025 [cited 2025 Sep 07];10(3):149-157. Available from: https://doi.org/10.18231/j.ijodr.2024.029
APA
Konda, P., Rafiq, A. M. (2025). 3D printing: Changing the landscape of orthodontics. IP Indian J Orthod Dentofacial Res, 10(3), 149-157. https://doi.org/10.18231/j.ijodr.2024.029
MLA
Konda, Prasad, Rafiq, Afaf Mohammed. "3D printing: Changing the landscape of orthodontics." IP Indian J Orthod Dentofacial Res, vol. 10, no. 3, 2025, pp. 149-157. https://doi.org/10.18231/j.ijodr.2024.029
Chicago
Konda, P., Rafiq, A. M.. "3D printing: Changing the landscape of orthodontics." IP Indian J Orthod Dentofacial Res 10, no. 3 (2025): 149-157. https://doi.org/10.18231/j.ijodr.2024.029