- Visibility 48 Views
- Downloads 12 Downloads
- DOI 10.18231/j.ijodr.2021.034
-
CrossMark
- Citation
Thinking forward: 3-D printing in orthodontics
- Author Details:
-
Nausheer Ahmed
-
Shreya K Shetty *
-
Haritha Urukalan
-
Nikhil P M
-
Abrar Younus
-
Ranjan K R Bhat
Introduction
3-D printing which originated as a tool for rapid prototyping rapidly found its application in various fields of science and art and is recently being applied in the field of medicine, dentistry including surgery.
The word 3-D printing is used to describe a manufacturing method that builds objects layer by layer. This process is termed additive manufacturing, and can also be referred to as rapid prototyping.[1], [2]
This technology has remarkable applications in dentistry, and with newer innovations in 3-D imaging and designing technologies such as cone beam computed tomography and intraoral scanning, and CAD/CAM technologies, it will become of increasing importance.
With the radical development of 3-D printing in medicine and dentistry, 3-D printing guarantees better patient care and improves the clinician’s efficiency in providing better care.
3-D printing is capable of providing customized treatment based on an individual's anatomic records. It has been valuable to construct true–to–life models in the field of medicine and dentistry for educational, research, treatment, and surgical planning purposes.
In the field of dentistry, it has been incorporated into various treatment modalities.
This article reiterates applications and recent advances in 3-D printing technology applicable to orthodontia.
Hideo Kodama of the Nagoya Municipal Industrial Research Institute in Japan discovered a way to print layers of material to create a 3-D object in 1981. Sadly, Kodama failed to get his patent for the technology approved.
In 1986, Charles Hull an American, created a prototype for a process called stereolithography (SLA).[3]
Stereolithography uses STL format to interpret the data in a CAD file. The data interpreted includes information on size, shape, color, and thickness, and the texture of the object to be printed. Hull used acrylic-based materials which transformed from liquid to solidupon exposure to ultraviolet lights. Hull is known as “the father” of 3-D printing.[4]
Hull’s 3-D printing as described in the U.S patent is as follows
“Briefly, and in general terms, the present invention provides a new and improved system for generating a three-dimensional object by forming successive, adjacent, cross-sectional laminae of that object at the surface of a fluid medium capable of altering its physical state in response to appropriate synergistic stimulation, the successive laminae being automatically integrated as they are formed to define the desired three-dimensional object.”[5]
He established the company 3-D Systems which introduced the first commercially available 3-D printer named SLA-250 in 1988.[6]
Applications of 3-D Printing in Dentistry
Study models
The earliest application of 3-D printing was in the making of anatomic study models.[7]
CBCT along with 3-D printing technology has transformed diagnosis and treatment planning in the field of dentistry.[8], [9]
The CBCT provides volumetric data to the 3-D printer to produce a detailed model of the bone structure in question. This allows the clinician to gain a clear idea of unusual, or unfamiliar anatomy to draw up the most favorable treatment plan.
The ability to clearly understand the anatomy and to produce suitable cutting guides using the technology has paved the way for newer surgical approaches which are less invasive and have better predictable outcomes. In reconstructive surgeries, 3-D printing has been used to prepare customized reconstruction plates and prostheses. This can also be used as an alternative to invasive autologous bone grafting procedures.[10]
Applications in designing prosthesis
The use of intraoral optical scanners enables the development of precise virtual models of implant positions, prepared tooth surfaces, and even the complete dental arches. For prosthodontics rehabilitation, prosthesis and restoration can be designed using CAD software. The data of the designed prosthesis can be milled using CAD-CAM software or can be 3-D printed.[11]
Fabrication of metallic structures using 3-D printing can be achieved by either indirect methods like printing in burn-out resins or waxes for a lost-wax process or directly in metal alloys.[12]
Printing in resin/wax and then using a traditional casting approach is beneficial as there is a reduced need for post-processing procedures when compared to that in the direct 3-D printing of metal casting alloys.[13]
Printing directly in metals is found to be more expensive as they require the use of costly technologies[14] and also demand elaborate post-processing before components may be ready for use.
Though there is some amount of material wastage, milling is advantageous over printing as the material used is intrinsically homogeneous and unaffected by operating conditions. Milling requires little post-processing, and the equipment is by far less expensive.[11]
Applications in restorative dentistry
Intraoral scanners are increasingly being used to scan the prepared tooth surfaces. This has necessitated the employment of 3-D printers to make physical models from the scanned data.
Though it is not always necessary to prepare physical models16 for fabrication of restorations, the models required when veneering materials have to be added. The models are also needed for the display of the restorations even when these restorations and digitally fabricated.[11]
Orthognathic surgery
The success of orthognathic surgery hinges on accurate diagnosis and treatment planning.
Conventionally orthognathic surgery planning involves 2 stages- radiographic simulation with cephalometric planning and manipulation of physical dental models in the desired direction. This process is essential to establish a postoperative occlusion which is then used to fabricate a surgical wafer. 3-D imaging technologies like CT and CBCT provide accurate data to develop study models, both digital and physical which are required for treatment planning.
Simulated repositioning of jaws using digital study models can be performed and surgical wafers can be accurately fabricated using 3-D printing technology.
This eliminates the arduous process of plaster model making and facebow recording and in turn minimizes the errors and imprecisions.
The wafer fabrication stage involves virtual filling in the void between the upper and lower digital dental models in their final occlusal positions. After the approval of the digital surgical wafer by the technician and clinician, the surgical wafers can be 3-D printed prior to the surgery.[15]
Orthodontics
In orthodontics, computer-aided designing and manufacturing technologies along with 3-D printing are replacing traditional laboratory setup.
This necessitates a different workflow. With the digital workflow treatment planning, appliance designing and fabrication can be performed precisely and without delay.
The digitally printed models are durable and precise. They also enable corrections before printing.
With the use of digital software, an orthodontist can remove the existing brackets and appliances from the scanned dataset and design a new appliance. Thus, the orthodontist can deliver a new appliance immediately upon the removal of the old one. For example, the patient can be provided with a retainer immediately after debonding, eliminating the waiting period or perhaps a second visit. In case of breakage or loss of retainer, a replacement can be easily fabricated either by using printed models or from the digitally archived data.[16]
The Invisalign® system can digitally realign the patients’ teeth and make series of 3-D printed models for the manufacturing of ‘aligners’. These aligners progressively reposition the teeth over a period of several months.[17]
Yet another example for printing with multiple materials using orthodontic CAD software is manufacturing of indirect bracket-bonding splints, printed in rigid and flexible materials for precise bracket placement.[18]
With the aid of CAD/CAM software bracket, production and bracket positioning can be performed simultaneously.[19]
In neonates and infants with syndromes affecting the craniofacial region, it is crucial to begin the treatment at the earliest. Conventional alginate impression techniques in these patients could be life-threatening. Intraoral scanning followed by digital workflow can be a more suited option.[20]
With a fully digital workflow, complex appliances like Tübingen Palatal Plate (TPP) and palatal plates for infants can be fabricated accurately by rapid prototyping. This enables the prototype to be digitally altered as per clinical needs and as well eliminates the need for conventional impressions and physical models to fabricate the appliance.[21], [22]
With the use of virtual set-ups, customized bracket printing, and robotic wire-bending, Dr. Wiechmann created a fully customized lingual appliance over 15 years ago.
The desired treatment outcome was virtually set up and then fully customized brackets were digitally designed to conform to the lingual surface of the teeth and were then 3-D printed in wax and cast in gold. This has enabled the creation of low-profile brackets which are well tolerated by patients.
This technology has also been incorporated into the manufacturing of labial appliances with the introduction of Insignia 9 by ORMCO (Ormco, Glendora, CA, USA) as a system of customized labial appliances which are then indirectly bonded.
Indirect bonding trays are can be printed accordingly and then the brackets are simply placed into the positioning jigs for accurate positioning. This method has been shown to reduce chairside time as well as bracket positioning errors during indirect bonding. [23]
Scanners and printers
New intraoral scanners are rapidly being introduced into clinical practice.[24] Though the detailed description of all the available technologies is beyond the scope of this article, a brief listing of the available scanning and 3-D printing technologies is listed in [Table 1].
|
Confocal Laser Scanner Microscopy (CLSM) |
|
Optical triangulation |
Optical scanning technologies |
Optical Coherence Tomography (OCT |
|
Accordion Fringe Interferometry (AFI) |
|
Active Wavefront Sampling (AWS) |
|
|
|
iTero® |
Align Technology |
|
True Definition |
|
3M ESPE |
|
Lythos™ |
|
Ormco Corporation |
|
CS 3500 |
|
Carestream |
|
Optical Scanning systems: |
TRIOS® |
3Shape |
|
FastScan® |
|
IOS Technologies |
|
3-D progress |
|
MHT Optic research |
|
E4D Technologies |
|
Planmeca PlanScan® |
|
Desktop scanners: |
Ortho Insight 3-D™ (Motion View Software, LLC, Chattanooga TN) |
|
VECTRA M3 Imaging System |
|
3-DMDface System (3-DMD, Atlanta, GA, USA) |
Facial scanners : |
Rainbow 3-D Camera (Genex Technologies, Inc., Kensington, MD, USA),
|
|
3-D Vectra (Canfield Imaging Systems, Fairfield, NJ, USA) |
|
Facial Insight 3-D (Motion View Software, LLC, Chattanooga TN, USA) |
Fused Deposition Modelling (FDM) |
|
Selective Laser Melting (SLM) |
|
Selective Laser Sintering (SLS) |
|
Electron Beam Melting (EBM) |
|
3-D printing technologies : |
Stereolithography (SLA) |
Inkjet 3-D printing |
|
Digital Light Processing (DLP) |
|
Laminated Object Manufacturing (LOM) |
|
Objet 30 Ortho Desk (Stratasys, Ltd., Eden Prairie, MI) |
|
ProJet® 3510 MP (3-D Systems, Rock Hill, SC) |
|
3-D printers in commonly used in orthodontics: |
ULTRA® 3SP™ Ortho (EnvisionTEC, Gladbeck, Germany, SC) |
Perfactory® Micro Ortho (EnvisionTEC, Gladbeck, Germany) |
|
Maker Bot Replicator 2 (Stratasys, Ltd., Eden Prairie, MI) |
|
FORMIGA P 110 (EOS, Munich, Germany) |
Review of recent literature involving 3-D printing technology incorporated into orthodontics
In a study conducted to compare 5-axis machining and 3-D printing it was observed that 5-axis machining can achieve the 0.01–0.02 mm accuracy level that is required by the dental industry standard. However, a 5-axis milling machine can fabricate only one model at once. Conversely, 3-D printing though less accurate (about 0.03–0.05 mm) had the advantage of multiple simultaneous productions.[25]
A study was conducted to evaluate the accuracy of a model made using the computer-aided design/computer-aided manufacture (CAD/CAM) milling method and 3-D printing method and to confirm its applicability as a working model for dental prosthesis production. This study concluded that the accuracy of the 3-D printing method is superior to that of the milling method.[26]
A study was conducted to determine the possibility of implementing a fully digital workflow clinically with individually designed and three-dimensional printed (3D-printed) brackets. This study concluded that it is possible to perform treatment with an individualized 3D-printed brackets system by using the proposed fully digital workflow.[27]
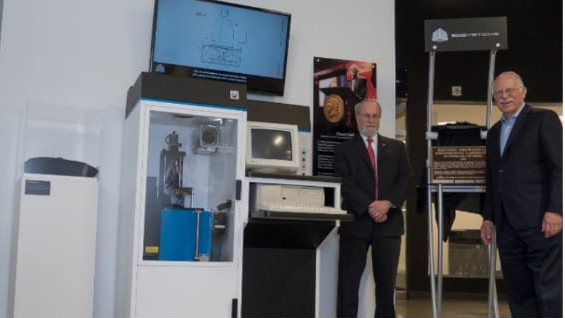
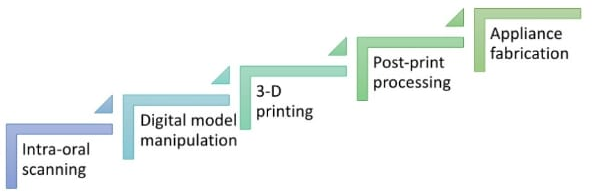
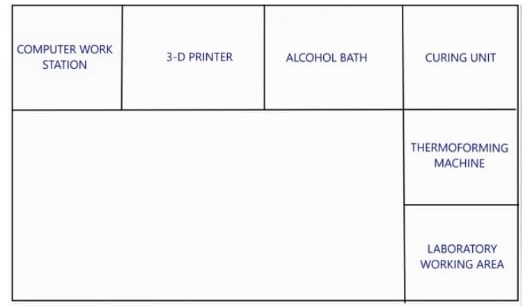
Digital workflow
Intra-oral scanning
Using intra-oral scanner virtual models of teeth and soft tissues are obtained.
The data set is exported as a standard tessellation language (STL) file.[29]
Digital model manipulation
The virtual model obtained by scanning is hollow and wafer-thin. The models obtained from such data are too fragile and are not suitable for appliance fabrication. Therefore, the virtual models should be made bulky by in-filling before printing. The base does not have to be as bulky as the conventional model but should be flat and provide essential stability to the model. Any suitable CAD software can be used for this purpose.
Several steps are involved in the digital manipulation of a virtual model using 3-D design software. They are as follows:
Identification of surface irregularities and repair of the surface
Attaining uniform model edges by removing unimportant soft tissue segments.
Designing a flat base parallel to the occlusal plane.
Adjusting the base height to avoid excessive model thickness thus reducing printing time and material wastage.
In-filling of the model. This adds sufficient bulk to the model and avoids disintegration during printing and appliance fabrication.
On the other hand, the model can be hollowed leaving sufficient thickness. This is suitable for models requiring full palate depth. This avoids excessive resin usage.
Labeling of the model should be done for patient identification.[29]
3-D printing
3-D printers differ from each other in terms of:
Size of the build platform and number of models printable in one print cycle
Print platforms may be cataloged as small, medium, and large.
Printers with small platforms allow relatively rapid printing of several horizontal models. These printers require the models to be thin and are suitable for the fabrication of aligners and retainers. These are not recommended for models in which full palatal depth is required for appliance fabrication. In clinical orthodontic practice, a medium-size printer is adequate.
For dental laboratories which requires printing of a large number of retainers and aligner models, large printers specifically designed for use in dentistry are apt. [29]
Printing speed and resolution
Speed and resolution are interdependent. With a higher resolution setting greater surface detail and smoother finish is obtained. This is due to an increase in the number of print layers. Hence, a longer time is required to print high-resolution data.[29]
Overall, 100-μm layer thickness appears to be adequate for the orthodontic purpose, when compared to slower print times with resolutions of 25μm and 50μm.[30]
The orientation of the models on the build platform also influences the speed. Models oriented parallel to the platform is printed faster.
Print times for dental models, at the 100-μm resolution, are commonly in the range of 1–10 hours, depending on horizontal and vertical model set-ups, respectively.
With a shorter print time, it is possible to deliver the appliances on the same day after post-processing and appliance fabrication.
Supports
To add to the structural integrity of the models, bars are incorporated into the model design. These bars are called supports. They are helpful when the model base is irregular. Supports do not have a standard measurement of density. They are usually added by the software automatically. An increased number of supports does not necessarily mean an increase in print time. They enable the safe removal of the model from the print platform. On the other hand, an increased number of supports requires more resin and a greater finishing.
User-friendliness of the printer software
The software used can automatically decide the orientation, support addition required for printing. The software can be used by the orthodontist from a different place to make any additional alterations. The data can be stored in the software and reprinted if the need arises. [29]
Post-print processing
Post–print processing generally involves the following steps.
Washing the models
The printed models should be rinsed thoroughly using 95% isopropyl alcohol in an ultrasonic bath for 10 minutes. This process removes any uncured surface resin. The models should be air-dried for removal of any residual isopropyl alcohol.
Curing the models
For complete curing of the resin, the model has to be exposed to ultraviolet and heat. Special curing units are usually provided by printer manufacturers to serve this purpose. The curing parameters should be set according to the manufactures instruction. Once the model is completely cured, it can be handled without gloves. [29]
Appliance fabrication
This stage is similar to that of conventional appliance making. To fabricate retainers of aligners a vacuum forming machine is used with a suitable thermoplastic material.
How to set up a digital laboratory?
The digital laboratory unlike the conventional laboratory does not require a stone dispenser, investment vibrator, model trimmer, large sink with plaster trap, or designated countertop space for poured casts. Instead, it requires space for a computer workstation with CAD/CAM software, the 3-D printers and resin cartridges, and the post-processing procedures.[16] Appropriate CAD and printing technology should be purchased as per use. The lab should be well ventilated, free from dust and disturbances. For the working of the thermoplastic machine compressed air is necessary. Compressed air is also required for cleaning freshly printed models. The working area depends on the type of printing technology used. Post-processing phases are different for different technology used. Appropriate equipment and a washing area have to be constructed.
Advantages
Adopting a digital workflow has numerous benefits. For instance, it takes a smaller number of appointments with shorter appointment time with increased patient comfort.[16] This improves patient compliance. The traditional plaster models are predisposed to clinical and procedural errors due to damage and distortion of impression. Technical errors like improper mixing of materials resulting in thin casts, porosities, chalky surface, improper trimming of the margins can occur it is time-consuming to manually prepare good plaster models. These models are susceptible to damage during transport and processing.
All the above problems can be eliminated by 3-D printing. 3-D printed models are accurate, stable, durable, and tolerates processing procedures of appliance fabrication well. These models can be easily reprinted if required as the data is digitally stored. The digital workflow allows modifications in the data set of the archived impression as per the clinical needs. Ex. Tooth movement can be simulated in aligner therapy before fabrication of the appliance. Brackets and bands can be digitally removed from the data before the fabrication of any appliance or retainers. The use of digital workflow saves time and expenditures due to outsourcing for appliance fabrication.
Disadvantages
Digital in-office lab has a high cost of maintenance. The printers require an annual subscription to CAD/CAM software.
Soldering of the appliances while placed on a resin model results in model distortion and there arises a need to replicate the model. To avoid this laser welding is advised over soldering, this is an add-on expense. Special training of the staff to familiarize them with 3-D software and hardware is required. Adequate training and knowledge are required in order to prepare digital models without printing and post-processing errors. Uncured resins and cleaning solvents can be irritating to the skin.[29] All health and safety guidelines should be followed during the handling and storage of these materials.
The costs and benefits of establishing an in-house digital lab should be carefully assessed and outsourcing should be considered if found economical.
3-D printing during COVID-19 pandemic
On 31st December 2019, 27 cases of pneumonia of unknown etiology were identified in Wuhan City, Hubei province in China. [31]
The Chinese Centre for Disease Control and Prevention (CCDC) analyzed the throat swab cultures and identified the causative agent which was subsequently named Severe Acute Respiratory Syndrome Coronavirus 2 (SARS-CoV-2).
On 30th January 2020, the WHO declared the outbreak of COVID-19 to be a Public Health Emergency of International Concern. [32]
Following this various guidelines for prevention and control of this disease were issued by multiple public health agencies and local health authorities.
These guidelines included social distancing, use of frequent hand hygiene, and masks.
Orthodontic patients are required to have routine follow-up visitations to the dental office.
With multiple travel restrictions imposed and apprehension of contacting the infection, patients often find regular dental visitations challenging. Many patients happen to miss their appointments, leading to unwanted treatment results and delayed conclusion of the treatment.[33]
Though clear aligner therapy are advantageous in the COVID-19 era, orthodontists must be fully aware of the limitations of aligners over tooth movement control.[34]
The following are some of the advantages offered by aligner therapy[35], [36], [37], [38], [39], [40]
Aesthetically pleasing
Better oral hygiene
Removable
Better in terms of comfort
Can be used for a variety of cases
Invisible attachments
Beneficial for intrusion and expansion
By delivering complete aligner sets upfront, the orthodontist can monitor the treatment progress virtually and recall the patient to the dental office only when required.
Use of in-house aligners may prove to be more economical over the long run, and also ensure that the patients' treatment goes on as planned with predictable tooth movements. [34]
The use of an in-house 3-D printer minimizes the need for frequent patient visitations as the data once scanned are archived with which appliances and retainers can be rapidly fabricated.
Conclusion
Incorporating 3-D printing into orthodontics enhances a simple and consistent workflow. It is with 3-D printing, orthodontics appliances can be manufactured at dramatically increased speed and accuracy with reduced material wastage. 3-D printing in dentistry is already an established industry, and observes continued progress. Constantly emerging newer applications hope to overcome the current shortcomings and make 3-D printing a routine and affordable solution for most clinical needs.
Source of Funding
None.
Conflict of Interest
The authors declare no conflict of interest.
References
- V Andonović, G Vrtanoski. Growing rapid prototyping as a technology in dental medicine. Mech Eng Sci J 2010. [Google Scholar]
- Q Liu, MC Leu, S Schmitt. Rapid prototyping in dentistry: technology and application. Int J Adv Manuf Technol 2006. [Google Scholar]
- . . . [Google Scholar]
- CL Ventola. Medical Applications for 3D Printing: Current and Projected Uses. P T 2014. [Google Scholar]
- C Hull. Apparatus for Production of Three-Dimensional Object by Stereolithography. US Patent 1986. [Google Scholar]
- . 3D Printing: What You Need to Know. PCMag.com . [Google Scholar]
- SN Kurenov, C Ionita, D Sammons, TL Demmy. Three-dimensional printing to facilitate anatomic study, device development, simulation, and planning in thoracic surgery. J Thorac Cardiovasc Surg 2015. [Google Scholar]
- HL Chan, K Misch, HL Wang. Dental imaging in implant treatment planning. Implant Dent 2010. [Google Scholar]
- P Worthington, J Rubenstein, DC Hatcher. The role of cone-beam computed tomography in the planning and placement of implants. J Am Dent Assoc 2010. [Google Scholar]
- PY Yun. The application of three-dimensional printing techniques in the field of oral and maxillofacial surgery. J Korean Assoc Oral Maxillofac Surg 2015. [Google Scholar]
- A Dawood, BM Marti, V Sauret-Jackson, A Darwood. 3D printing in dentistry. Br Dent J 2015. [Google Scholar]
- KV Venkatesh, VV Nandini. Direct metal laser sintering: a digitised metal casting technology. J Indian Prosthodont Soc 2013. [Google Scholar]
- M Kasparova, L Grafova, P Dvorak, T Dostalova, A Prochazka, H Eliasova. Possibility of reconstruction of dental plaster cast from 3D digital study models. Biomed Eng Online 2013. [Google Scholar]
- A Örtorp, D Jönsson, A Mouhsen. Vult von Steyern P. The fit of cobalt-chromium three-unit fixed dental prostheses fabricated with four different techniques: a comparative in vitro study. Dent Mater 2011. [Google Scholar]
- RR Cousley, MJ Turner. Digital model planning and computerized fabrication of orthognathic surgery wafers. J Orthod 2014. [Google Scholar]
- C Groth, ND Kravitz, JM Shirck. Incorporating three-dimensional printing in orthodontics. J Clin Orthod 2018. [Google Scholar]
- O Tuncay. . The Invisalign System 2006. [Google Scholar]
- F Ciuffolo, E Epifania, G Duranti, V De Luca, D Raviglia, S Rezza. Rapid prototyping: a new method of preparing trays for indirect bonding. Am J Orthod Dentofacial Orthop 2006. [Google Scholar]
- S Nayar, S Bhuminathan, WM Bhat. Rapid prototyping and stereolithography in dentistry. J Pharm Bioallied Sci 2015. [Google Scholar]
- RA Chate. A report on the hazards encountered when taking neonatal cleft palate impressions (1983-1992). Br J Orthod 1995. [Google Scholar]
- AB Xepapadeas, C Weise, K Frank, S Spintzyk, CF Poets, C Wiechers. Technical note on introducing a digital workflow for newborns with craniofacial anomalies based on intraoral scans - part I: 3D printed and milled palatal stimulation plate for trisomy 21. BMC Oral Health 2020. [Google Scholar]
- AB Xepapadeas, C Weise, K Frank, S Spintzyk, CF Poets, C Wiechers. Technical note on introducing a digital workflow for newborns with craniofacial anomalies based on intraoral scans - part II: 3D printed Tübingen palatal plate prototype for newborns with Robin sequence. BMC Oral Health 2020. [Google Scholar]
- NE Tarraf, DM Ali. Present and the future of digital orthodontics. Semin Orthod 2018. [Google Scholar]
- ED Taneva, BKC Evans. 3D scanning, imaging, and printing in orthodontics. Issues in Contemporary Orthodontics 2015. [Google Scholar]
- H Yau, TJ Yang, YK Lin. Comparison of 3-D Printing and 5-axis Milling for the Production of Dental e-models from Intra-oral Scanning. Comput aided Des Appl 2016. [Google Scholar]
- YG Jeong, WS Lee, KB Lee. Accuracy evaluation of dental models manufactured by CAD/CAM milling method and 3D printing method. J Adv Prosthod 2018. [Google Scholar]
- KF Krey, N Darkazanly, R Kühnert, S Ruge. 3D-printed orthodontic brackets - proof of concept. Int J Comput Dent 2016. [Google Scholar]
- . . . [Google Scholar]
- RR Cousley. Introducing 3D printing in your orthodontic practice. J Orthod 2020. [Google Scholar]
- CS Favero, JD English, BE Cozad, JO Wirthlin, MM Short, FK Kasper. Effect of print layer height and printer type on the accuracy of 3-dimensional printed orthodontic models. Am J Orthod Dentofacial Orthop 2017. [Google Scholar]
- H Lu, CW Stratton, YW Tang. Outbreak of pneumonia of unknown etiology in Wuhan, China: The mystery and the miracle. J Med Virol 2020. [Google Scholar]
- C Sohrabi, Z Alsafi, N O'neill, M Khan, A Kerwan, A Al-Jabir. World Health Organization declares global emergency: A review of the 2019 novel coronavirus (COVID-19). Int J Surg 2020. [Google Scholar]
- A Marya, A Venugopal, N Vaid, MK Alam, MI Karobari. Essential Attributes of Clear Aligner Therapy in terms of Appliance Configuration, Hygiene, and Pain Levels during the Pandemic: A Brief Review. Pain Res Manag 2020. [Google Scholar]
- Y Liu. Advantages and disadvantages of clear aligner treatment in orthodontics. Zhonghua Kou Qiang Yi Xue Za Zhi 2009. [Google Scholar]
- CT Drake, SP Mcgorray, C Dolce, M Nair, TT Wheeler. Orthodontic tooth movement with clear aligners. ISRN Dent 2012. [Google Scholar]
- R Zhao, R Huang, H Long, Y Li, M Gao, W Lai. The dynamics of the oral microbiome and oral health among patients receiving clear aligner orthodontic treatment. Oral Dis 2020. [Google Scholar]
- MF Sfondrini, P Gandini, R Alcozer, PK Vallittu, A Scribante. Failure load and stress analysis of orthodontic miniscrews with different transmucosal collar diameter. J Mech Behav Biomed Mater 2018. [Google Scholar]
- N Haouili, ND Kravitz, NR Vaid, DJ Ferguson, L Makki. Has Invisalign improved? A prospective follow-up study on the efficacy of tooth movement with Invisalign. Am J Orthod Dentofacial Orthop 2020. [Google Scholar]
- F Garino, T Castroflorio, S Daher. Effectiveness of composite attachments in controlling upper-molar movement with aligners. J Clin Orthod 2016. [Google Scholar]
- M Tepedino, V Paoloni, P Cozza, C Chimenti. Movement of anterior teeth using clear aligners: a three-dimensional, retrospective evaluation. Prog Orthod 2018. [Google Scholar]
- Introduction
- Applications of 3-D Printing in Dentistry
- Study models
- Applications in designing prosthesis
- Applications in restorative dentistry
- Orthognathic surgery
- Orthodontics
- Scanners and printers
- Review of recent literature involving 3-D printing technology incorporated into orthodontics
- Digital workflow
- Intra-oral scanning
- Digital model manipulation
- 3-D printing
- Size of the build platform and number of models printable in one print cycle
- Printing speed and resolution
- Supports
- User-friendliness of the printer software
- Post-print processing
- Appliance fabrication
- How to set up a digital laboratory?
- Advantages
- Disadvantages
- 3-D printing during COVID-19 pandemic
- Conclusion
- Source of Funding
- Conflict of Interest